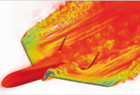
Proceedings
home
preface
contents
authors
keywords
copyright
reference
©2012 Civil-Comp Ltd |
 |
 |
 |
W. Habchi and J. Issa
Department of Industrial and Mechanical Engineering, Lebanese American University, Byblos, Lebanon
Keywords: elastohydrodynamic lubrication, finite elements, model reduction, full system approach.
full paper (pdf) -
reference
Numerical modeling of the elastohydrodynamic lubrication (EHL) problem has always faced major difficulties that have lead throughout the years to the introduction of different numerical approaches [1]. These difficulties stem from the high nonlinearity of the Reynolds equation governing the hydrodynamic part of the problem and the coupling between the elastic and hydrodynamic parts. The ultimate aim of any EHL solver is to provide robust, fast and accurate solutions over a large range of operating conditions. In recent work, Habchi et al. [2,3] introduced a finite element full-system approach where the elastic deflection calculations were based on a linear elasticity model. A stabilized Galerkin least squares (GLS) formulation was introduced for the solution of highly loaded contacts where the high nonlinearity of the Reynolds equations leads to spurious oscillations in its solution when a standard Galerkin formulation is employed. This model was shown to have the same complexity as state of the art models. In addition, the use of a full-system approach leads to much faster convergence rates and the finite element discretization of the problem enabled non-regular non-structured meshing which leads to smaller size matrix systems. Hence, faster CPU times were obtained compared with state-of-the-art models. Yet, a major improvement is possible to further reduce the CPU time consumption for this model. In fact, the elastic deflection of the solid elements is computed by means of a linear elasticity approach. The latter is applied to the entire solid domain, whereas for the EHL solution, only the surface deflection in the contact area is required. Hence, the large number of degrees of freedom that are being computed is not useful in practice. This paper introduces a model order reduction technique to improve the elastic deflection calculation by reducing the size of the corresponding model. The reduced model is shown to be much more efficient than the full one, requiring only a few degrees of freedom to analyse the elastic deformation of the solid components. In addition, a comparison with the full model shows an order of magnitude CPU time gain with errors of the order of only 1 for the central and minimum film thicknesses.
- 1
- D. Dowson, P. Ehret, "Past, Present and Future Studies in Elastohydrodynamics", IMechE Part J, J. Eng. Trib., 213(5), 317-333, 1999.
- 2
- W. Habchi, D. Eyheramendy, P. Vergne, G. Morales-Espejel, "Stabilized Finite Elements for Elastohydrodynamic Lubrication Problems", in M. Papadrakakis, B.H.V. Topping, (Editors), "Proceedings of the Sixth International Conference on Engineering Computational Technology", Civil-Comp Press, Stirlingshire, UK, Paper 19, 2008. doi:10.4203/ccp.89.19
- 3
- W. Habchi, D. Eyheramendy, P. Vergne, G. Morales-Espejel, "Stabilized Fully-Coupled Finite Elements for Elastohydrodynamic Lubrication Problems", Int. J. of Adv. in Eng. Software, 2010. doi:10.1016 /j.advengsoft.2010.09.010
|