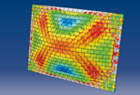
Proceedings
home
preface
contents
authors
keywords
copyright
reference
©2012 Civil-Comp Ltd |
 |
 |
 |
J. Atkociunas and G. Blazevicius
Department of Structural Mechanics, Vilnius Gediminas Technical University, Lithuania
Keywords: optimal shakedown design, elastic-plastic truss, standards, mathematical programming.
full paper (pdf) -
reference
The buckling resistance of truss elements under compression is determined according to the requirements of standards such as the Eurocode (EC). The element loses its stability, which implies that the ultimate limit state is violated, when the design value of a compression force exceeds the resistance value of an element. When mathematical programming is used for optimal perfectly elastic-plastic truss design, the complementary slackness conditions of mathematical programming are written with the help of plastic multipliers [1]. These multipliers are used for evaluating the residual forces, therefore, their accurate determination makes the main stage of the solution of the problem. In this paper, new conditions, which complement the optimization problem and enhance the interpretation of the stability constraints in the shakedown process, are presented. Plastic deformations of the compression members after the loss of stability are not defined in the EC and, therefore, cannot be evaluated. Thus, the above-mentioned complementary slackness conditions are not adequate to ensure the correct evaluation of plastic deformations in the shakedown process. The proposed new formulation solves this problem by ensuring that plastic deformations (in the form of plastic multipliers) could only emerge as a result of the development of the tension yield stress or compression yield stress of very stocky elements. Slender elements under compression are checked for loss of stability and cannot reach the yield stress (and, therefore, cannot produce nonzero plastic multipliers).
In the Eurocode standards, all design calculations are divided into two groups, aimed at verifying the ultimate and serviceability limit states. Two different reliability levels are used to describe these limit states. When the stability and strength conditions of the mathematical model are included for the ultimate limit state verification, the serviceability limit state for the structure must be secured as well. Therefore, the stiffness conditions must be introduced into the model [2]. The displacements of a perfectly elastic-plastic truss consist of residual and quasi-elastic components. According to the use of the suggested methodology, the residual component occurs during the shakedown process, therefore, it depends on the ultimate limit state with high level reliability. The quasi-elastic component is calculated, using Hooke's law and depends on the serviceability limit state with the lower level reliability. The dual reliability level approach is based on the Eurocode recommendations, allowing for the design of a more economical structure. The numerical example of truss optimization, based on using the improved mathematical model, is presented.
-
- 1
- J. Atkociunas, A. Venskus, "Optimal shakedown shakedown design of frames under stability conditions according to standards", Computers and Structures, 89, 435-443, 2011.
- 2
- S. Kaliszky, J. Lógó, "Plastic behavior and stability constrains in the shakedown analysis and optimal design of trusses", Structural and Multidisciplinary Optimization, 24, 118-124, 2002.
|