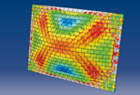
Proceedings
home
preface
contents
authors
keywords
copyright
reference
©2012 Civil-Comp Ltd |
 |
 |
 |
N. Cocheteau1, F. Lebon1, I. Rosu1, A. Maurel1, S. AitZaid2 and I. Savin DeLarclause2
1Laboratory of Mechanic and Acoustics, University of Aix-Marseille, France
2National Centre for Spatial Studies, Toulouse, France
Keywords: silicon direct bonding, modelling, finite element, surface energy, roughness, mechanical tests.
full paper (pdf) -
reference
Direct bonding is a widely used process is microelectronics and increasingly on terrestrial and spatial optics. This bonding process is based on the contacting of two well-polished surfaces without the use of any adhesive or additional materials. Bonding is the result of interatomic bonds such as van der Waals or hydrogen bonds. This process requires a very precise physical preparations of surface (flatness and roughness controls), surface cleaning by solvents and finally thermal treatment (annealing) in order to increase the mechanical resistance of the bonded interface [1,2].
Despite many advantages such as high precision and dimensional stability of the assemblies, direct bonding is poorly reproducible. In addition, constraints involved in spatial application of the process (thermal fatigue, vibration, etc.) require the improvement of the mechanical performances of adhesive bonds.
Consequently, chemical and mechanical tests such as surface wettability, X-ray photoelectron spectroscopy or double shear tests were performed in order to characterize interfaces and observe the influence of the annealing. The results of analyses show the reversibility of the process, and an increase of the bonding energy with temperature.
The aim of this study, reported in this paper, was therefore to compare the various ways of modelling this particular type of adhesive contact in the framework of finite element methods. Classical models, such as the virtual crack closure technique [3,4,5] and cohesive elements models, and models in which adhesion is combined with cohesive elements are therefore compared [6,7,8,9].
-
- 1
- Q.T. Tong, U. Gössele, "Semiconductor wafer bonding: recent developments", Material Chemistry and Physics, 37, 101-107, 1994.
- 2
- A. Ploßl, G. Krauter, "Wafer direct bonding: Tailoring adhesion between brittle materials", Materials Science and Engineering, 25, 1-88, 1999.
- 3
- V. Ranatunga, "Finite Element Modeling of Delamination crack propagation in laminated composites", Proceedings of the world congress on Engineering, vol III, 2011.
- 4
- A. Leski, "Implementation of the virtual crack closure technique in engineering FR calculations", Finite element in analysis and design, 43, 261-268, 2007.
- 5
- A.B. de Morais et al., "Analysis of crack propagation in double cantilever beam test of multidirectional laminates", Mechanics of materials, 35, 641-652, 2003.
- 6
- G. Liao et al., "Effect of surface characteristic on room temperature silicon direct bonding", Sensors and Actuators A, 158, 335-341, 2010.
- 7
- C. Gui et al., "The effect of surface roughness on direct wafer bonding", Journal of applied physics, 85(10), 7448-7454, 1999.
- 8
- K.L. Johnson, "The adhesion of two elastic bodies with slightly wavy surfaces", International Journal of Solids and Structures, 32(3/4), 423-430, 1995.
- 9
- B.A. Galanov, "Models of adhesive contact between rough elastic solids", International Journal of Mechanical Science, 2011.
|