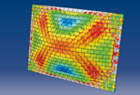
Proceedings
home
preface
contents
authors
keywords
copyright
reference
©2012 Civil-Comp Ltd |
 |
 |
 |
A.L.L. Silva1, A.M.P. Jesus2 and A.A. Fernandes1
1Faculty of Engineering, Porto University, Portugal
2University of Trás-os-Montes e Alto Douro, Portugal
Keywords: fatigue analysis, local approaches, welded joints, riveted joints, numerical analysis, finite element method, submodelling process.
full paper (pdf) -
reference
Nowadays, several alternative procedures have been proposed for fatigue assessment of structural details. Nevertheless, the nominal stress (SN) approach is the basis of the main design codes. This paper presents a numerical approach for the application of the local fatigue analysis of representative details from two Portuguese railway bridge details. Two relevant types of joints are modelled using the finite element method (FEM).
The first case study consists of a riveted connection from the metallic railway Trezói bridge, which was inaugurated in 1956. A continuous finite element models were proposed. The boundary conditions are provided by a global dynamic finite element model of the bridge and applied to the local finite element model using the multi-point constraint (MPC) technology. In general, the fatigue damage values are low for the investigated locations, leading to a significant number of train crossings. Nevertheless, the lower number of strain crossings to initiate a crack was about 4.45x105 and was obtained for the stringer-to-gusset connection. The horizontal bracing-to-gusset connection and the stringer-to-gusset connection have been revealed to be more critical. These conclusions may be influenced by the fact that full continuity was assumed between the plates and members which, in reality, are joined by rivets.
The other case study consists on the Alcácer do Sal Railway Bridge, which is a steel-concrete composite bridge inaugurated in 2010. Three representative welded details are modelled and used to perform a fatigue damage analysis taking into account distinct dynamic train loads of increasing severity. For these models, a submodelling process was used to provide the boundary conditions necessary to model several train crossings. Some fillet welded joints were analysed in order to compute relevant structural stress spectra for damage assessment. The procedure of stress linearization across the whole thickness was selected to compute the structural stress at the weld toe. The resulting membrane plus bending stresses were computed in a direction normal to the weld, at the weld toe location. The weld joint that shows higher stress level is located in the detail A, which is a non-classed welded joint where the higher structural stress level was found. However, the structural stresses are quite low (less than 25MPa), being below the damage threshold.
|