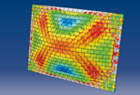
Proceedings
home
preface
contents
authors
keywords
copyright
reference
©2012 Civil-Comp Ltd |
 |
 |
 |
L. Dlouhý1 and M. Lepš2
1Faculty of Civil Engineering, Brno University of Technology, Czech Republic
2Faculty of Civil Engineering, Czech Technical University in Prague, Czech Republic
Keywords: post-tensioned concrete, design, bridge, cost, optimization, evolutionary algorithms, genetic algorithms.
full paper (pdf) -
reference
Generally, the technology of post-tensioned concrete is commonly used in the construction of medium and long span concrete bridges all around the world. An opportunity for the active modification of the distribution of the internal forces offered by variable geometry of post-tensioned tendons is one of the main advantages. Unfortunately these types of structure are not usually investigated as optimization tasks. This is caused by the complexity of the structure and a presence of many design variables which are often discrete. This paper presents one of the first examples of the optimum design of tendon geometry of three span post-tensioned concrete structures that includes the necessary design details as well as the inclusion of discrete variables.
In this paper, a post-tensioned concrete three span bridge is optimized from the prestressing level as well as the geometry point of view. The cross-sectional shape is three-beam with fixed dimensions of depth and width. The design and checking of the structure is performed according to the Eurocodes. The structure is analysed incorporating the construction stages with a time dependent analysis of creep and shrinkage behaviour according to Annex B from EN 1992-1-1 for a 100 year life time. The objective of the study, presented in this paper, is to minimize a necessary area of prestressing reinforcement while still satisfying all constraints. A serviceability limit state (crack appearance using a check of allowable concrete stresses on a characteristic combination) and an ultimate limit state (the check of capacity calculated in terms of the interaction diagram for the acting combination of a normal force and a bending moment) were evaluated as constraints. Limit values of checks (a ratio of the calculated and the limit values) were selected in a standard way as 1.0.
Because the numbers of strands are discrete design variables, it is necessary to apply an optimization method which is able to handle the discrete type of parameters. Here, modified simulated annealing or differential evolution methods can be used. Both methods were tested and finally, modified simulated annealing has been selected as a result of its faster convergence. The amount of prestressing reinforcement obtained was decreased by 24% in comparison to the original design.
|