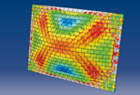
Proceedings
home
preface
contents
authors
keywords
copyright
reference
©2012 Civil-Comp Ltd |
 |
 |
 |
M. Leite1, J.F.A. Madeira2,3, A. Silva1,4, E. Henriques2 and R. Roth5
1ICEMS, Institute of Materials and Surfaces Science and Engineering, 2IDMEC, Institute of Mechanical Engineering,
IST, Instituto Superior Técnico, Lisbon, Portugal
3ISEL, Instituto Superior de Engenharia de Lisboa, Portugal
4Granta Design Limited, Cambridge, United Kingdom
5MSL, Materials Systems Laboratory, MIT, Massachusetts Institute of Technology, Cambridge, USA
Keywords: materials selection, multiple parts, automotive, direct search, multiobjective optimization.
full paper (pdf) -
reference
Materials selection is a matter of great importance to engineering design and software tools are valuable to inform decisions in product development. When a pool of alternative materials is available for different parts, the question of what optimal material mix to select for a set of parts is not simple. The number of available materials in engineering design is great and different materials and shapes can concur in a final design. If the number of parts to be selected is small, the problem is somewhat trivial, but if the number of parts increases, there is a problem of alignment between materials selection and product attributes.
In engineering problems, the designer decides about the part shape and material and the decisions taken largely determines the part cost and weight. However, it is only possible to calculate the cost and weight when the part geometric attributes and production parameters are defined.
As a result of the large number of permutations, exhaustive search is not possible justifying the use of an optimization procedure to determine the optimal solution. Another aspect of the optimization tool is that it needs to deal with non-differentiable objective functions and constraints. To solve this multi-objective optimization problem, a new routine based on direct multisearch (DMS) algorithm [1] was created.
An example from industry has been solved using this new methodology based on DMS. To illustrate the problem a case study of a sheet metal progressive stamping process was studied. In this example, there are fifty-five parts, each with a given geometry and material grade already suggested by an experienced designer. The role of the optimization tool is to find, from a pool of different cold rolled material grades and different thicknesses available, the optimum material selection of each part in the multi-part environment. The objective functions are two: the manufacturing cost of each part and the resulting weight of the set of parts. In addition, constraints such as manufacturability, strength and stiffness are taken in consideration to assure validity of the DMS results.
Results from the Pareto front can help the designer to align its materials selection for a complete set of materials with product attribute objectives, depending on the relative importance of each objective. The results illustrate the capacity of this DMS model to solve the optimization problem within a reasonable amount of time.
-
- 1
- A.L. Custodio, J.F.A. Madeira, A.I.F. Vaz, L.N. Vicente, "Direct Multisearch for Multiobjective Optimization", SIAM Journal on Optimization, 21(3), 1109-1140, 2011.
|