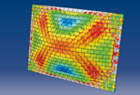
Proceedings
home
preface
contents
authors
keywords
copyright
reference
©2012 Civil-Comp Ltd |
 |
 |
 |
J.-W. Simon and S. Reese
Institute of Applied Mechanics, RWTH Aachen University, Germany
Keywords: fibre composites, delamination, debonding, orthotropic material model, solid-shell concept, enhanced strain formulation, reduced integration, hourglass stabilization.
full paper (pdf) -
reference
Fibre-reinforced composites are gaining more and more importance in technical applications as a result of their most beneficial characteristics: the very high Young's modulus and low density, which are particularly leveraged in shell-like structures of lightweight construction. The composites examined in this paper consist of multiple layers, each of which is composed of a woven fabric,with two families of fibres, embedded in a matrix material. To incorporate the anisotropic material behaviour of such composites, a micro-mechanically motivated orthotropic material model at finite strains is adopted, which is based on the concept of structural tensors representing the different fibre orientations.
Since delamination is a major failure mode of layered composites, predicting its initiation is essential for the design of composite structures. To evaluate the onset of delamination, a criterion is used in this paper, which is based on stress-strength relations. In particular, a quadratic interaction of the inter-laminar traction and the inter-laminar resultant shear is assumed, whereby mixed-mode loading situations are taken into account.
Clearly, investigating the initiation of delamination by means of stress-strength relations requires an accurate representation of the through-the-thickness stress distribution, which is delicate for thin shell-like structures. While solid elements exhibit only poor performance in shell-like applications, shell elements cannot represent appropriately the material behaviour. As a consequence, in this paper, a solid-shell finite element is utilised, which allows for incorporating the three-dimensional material model, still being suited for application to thin structures.
The current solid-shell formulation eliminates transverse shear locking, which is present in standard eight-node hexahedral elements, using the assumed natural strain (ANS) method. Further, applying the enhanced assumed strain (EAS) concept eliminates the volumetric locking in the case of (nearly) incompressible materials as well as the Poisson thickness locking, which occurs in bending problems of shell-like structures resulting from the non-constant distribution of transverse normal strain over the thickness. Moreover, the proposed element is numerically efficient owing to the reduced integration.
|