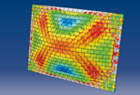
Proceedings
home
preface
contents
authors
keywords
copyright
reference
©2012 Civil-Comp Ltd |
 |
 |
 |
D. Weiss1 and S. Adriaenssens1,2
1Department of Civil and Environmental Engineering, Princeton University, Princeton NJ, United States of America
2MEMC, VUB, Brussels, Belgium
Keywords: thin shell, form finding, digitization, finite element.
full paper (pdf) -
reference
This paper presents a new design methodology that uses physical hanging plaster models and digital scanning techniques to appraise thin shell shapes in the preliminary design phase of a building project. The paper is divided into three parts.
The first part gives an overview of the use of physical models in the development of structurally efficient shell shapes. By discussing the work of Wren, Poleni and Gaudi on hanging chains and hanging net models. Then Ramaswamy's hanging textile formwork, Isler's polyester resin membrane models and finally Belles' models based on homeostasis are discussed. The advantages and shortcomings of the presented physical methods are outlined and suggestions as to how these disadvantages may be overcome are made.
The second part introduces the new design exploration methodology that consists of three phases: Phase i) the physical hanging plaster model making, Phase ii) the digitizing of the physically form of the found surface, and Phase iii) the appraisal of the shell surface in terms of stresses, deflections and buckling using the commercially available finite element software SAP 2000. Phase i) discusses in detail how to make successful hanging continuous shell models using cheesecloth and plaitre de Paris. The physical forms are compared with analytical results for hanging chains and proven to be very similar. In Phase ii) the physical model is digitally scanned using a hand held three-dimensional scanner. The scanning procedure is elaborated upon and suggestions as how to make this a successful operation are given. After scanning, the resultant triangulated mesh is manipulated in AutoCAD to overcome scaling and modelling issues with the goal of preparing the mesh for finite element analysis. In Phase iii) the numerical analysis reveals unexpected results for the stress plots which can be explained due to the insufficient accurate physical modelling and the scanning. However the deflection and buckling results prove to be well within the accepted limits defined by the American Building Code. The buckling results are further validated against analytical results.
The paper concludes, by discussing the successfulness of the presented methodology (most specifically in the context of shell shape design exploration) and makes suggestions for other domains of application.
|