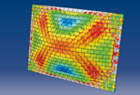
Proceedings
home
preface
contents
authors
keywords
copyright
reference
©2012 Civil-Comp Ltd |
 |
 |
 |
E. Vegueria, R. Ansola, J. Canales and A. Maturana
Deparment of Mechanical Engineering, University of the Basque Country, Bilbao, Spain
Keywords: optimization, compliant, mechanisms, microactuators, topology, evolutionary, thermal.
full paper (pdf) -
reference
This paper describes the design of compliant thermal microactuators subjected to non-uniform temperature fields using an evolutionary topology optimization procedure. Traditional compliant mechanisms work under the application of a force at an input port and generate the desired force or deflection at the output port as a result of their flexibility. Thermal micro actuators are those compliant mechanisms into which thermal loading is applied as an input instead of a force. These systems function based on the thermal expansion of the compliant mechanism material and efficiently convert very large forces, associated with thermal action, into deflection. They provide displacements of different points in the device through non-uniform temperature fields by virtue of their especially designed topology and shape. During recent decades topology optimization techniques have been shown to be efficient tools to conceive these kinds of distributed compliant mechanisms.
The procedure applied in this paper is based in the evolutionary structural optimization (ESO) method which has been successfully applied to several optimum material distribution problems such as control of local stress level, maximization of the stiffness, buckling or frequency. In previous work, this group has successfully applied this method for compliant mechanism optimization for directly applied input loads and for simple uniform temperature fields. This paper developes an extension of this procedure to approach the more complicated case of non-uniformly heated thermal microactuators. In order to obtain optimal solutions for the topology optimization of thermally actuated compliant mechanisms an additive version of the method is used.
The presence of checkerboard patterns causes difficulty in interpreting and manufacturing the solution obtained. Another problem related to topology optimization is the so-called mesh dependency problem that refers to the problem of obtaining different topologies when different finite element meshes are used. These problems are significantly avoided by introducing a filtering scheme. At the same time in order to stabilize the optimization process it the sensitivity numbers are averaged with its historical information.
The validity of this technique is demonstrated in an example and the designs obtained are compared favourably with the analytical solution calculated for the example. Further work will include the expansion of this topology optimization algorithm to incorporate complicated thermally actuated compliant mechanisms specifications, such as electro-thermal actuators subjected to non temperature fields derived from Joule heating, since supplying constant heat flux might not be efficient in practice.
Future investigation should explore the application of the bi-directional algorithm, which would help to yield a more stable convergence and a general behaviour closer to that of other optimization methods.
|